Efficient thermal and fluid management strategies for aerospace heat exchangers
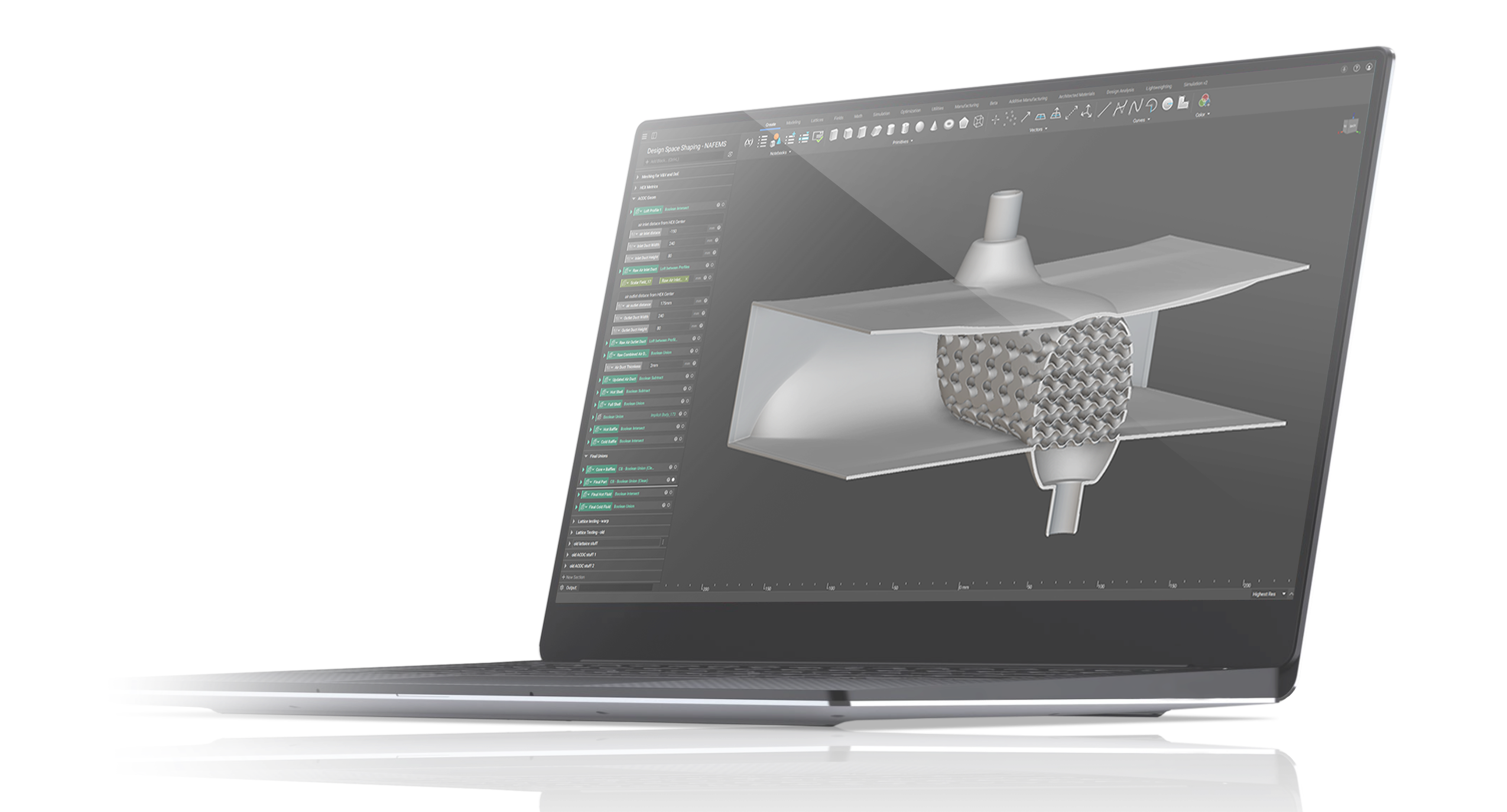
Written by Maiki Vlahinos
Published on October 23, 2023
Applications
Key Software Capabilities
- Design automation
- Implicit Interop
- Topology optimization
Discover heat exchangers' pivotal role in aerospace and why optimizing them should be a priority in your manufacturing and design strategy. Unlock strategies for streamlined thermal and fluid management so you can propel aerospace components' safety, efficiency, and longevity to new heights.
Heat exchangers play a pivotal role in advancing the aerospace and defense industry, ensuring peak system functionality. Their responsibilities range from optimizing engine performance to improving passenger comfort. With advanced tools like nTop, engineers can leverage additive manufacturing (AM) to design heat exchangers with unprecedented precision and performance.
This article offers an in-depth analysis of the intricacies of heat exchangers in aerospace applications, and delves into fluid and thermal management strategies. We’ll explore how the integration of software solutions like nTop can usher in a new era of design innovation.
Heat exchangers in aerospace applications
Heat exchangers are vital in aerospace and defense. They optimize engine performance, regulate electronic component temperatures, and ensure cabin comfort. They manage the thermal balance between engine fuel and lubricating oil, preventing oil overheating, lubrication issues, and cavitation, while also preparing fuel for optimal combustion.
Efficient thermal and fluid management in aerospace systems
Efficient thermal and fluid management strategies for heat exchangers offer several benefits, including:
- Safe temperatures: Effective thermal and fluid management helps maintain safe operating temperatures and pressures for critical components, lowering the risk of system failures and accidents.
- Energy efficiency: Heat and fluid management can increase the energy transferred within aerospace heat exchangers, thereby optimizing their performance and contributing to overall energy efficiency in aviation systems.
- Weight reduction: Efficient systems allow for the design of lighter heat exchangers and cooling systems, contributing to reduced aircraft weight and improved fuel efficiency.
Challenges in thermal and fluid management
Thermal and fluid management present challenges, notably concerning weight and retrofitting.
Mass and weight
In aerospace, even a small change in weight can make a significant impact. Components like heat exchangers and coolants play a vital role in aircraft performance and fuel efficiency. Engineers work to improve heat exchanger efficiency and reduce weight by exploring durable materials and weight-reduction methods like lattice structures.
Pressure drop is influenced by several factors such as length of a system, the presence of bends or turns, and the roughness of the interior surface. As these variables increase, the pressure drop within the system also increases, potentially reducing system efficiency and demanding more energy for fluid flow.
Retrofitting
Retrofitting older aircraft with modern heat exchanger components is a challenge in the aerospace sector due to space constraints and compatibility issues with existing systems. Engineers must sometimes design for enhanced thermal loads and fluid flow rates while preserving structural integrity and satisfying overall flow and system requirements.
Although increasing surface area can aid heat transfer, it can sometimes raise the pressure drop, detracting from system performance and efficiency. Retrofitting thus requires a balanced approach, combining innovation with pragmatism to ensure both efficiency and safety.
The power of TPMS and gyroid structures
Many shell and tube heat exchangers that are available off the shelf have reliable heat transfer capabilities, but they also have spatial and volumetric constraints. These designs have also seen little innovation over the decades. AM allows engineers to create advanced, lightweight structures such as triply periodic minimal surface (TPMS) lattices and gyroids that would be unachievable with traditional methods. These structures combine structural strength with efficient fluid pathways, enhancing thermal and fluid management.
- TPMS: Characterized by their superior strength-to-weight ratios and increased surface area to mass, TPMS are crucial for efficient material use and balancing fluid temperatures. They support fluid mixing, offer impressive stiffness, and can handle significant compressive loads with slender walls.
- Gyroid: This TPMS variation stands out for its structural strength, promoting efficient fluid movement while preserving balance. It represents a leap forward in aerospace design, ensuring optimal fluid pathways without sacrificing equilibrium.
Strategies for efficient thermal management
Enhanced heat transfer
TPMS and gyroid structures are known for their superior heat transfer abilities due to their increased surface area. With a 1:1 shared surface area, they excel at dissipating heat from vital components like engines and electronics. They inherently separate into two fluid domains which share a continuous volume in a compact envelope, making them ideal for heat exchangers.
Reduced weight
These novel structures can also decrease the weight of heat exchangers and cooling systems, thus improving fuel efficiency and extending the range of aircraft. This lightweighting technique is achieved by packing more surface area into a smaller or similar design space thanks to structures like TPMS, which use their intricate geometric properties to optimize the surface-to-material ratio. That allows them to efficiently dissipate heat and facilitate cooling, all while minimizing the overall material requirements.
The TPMS unit cell doesn’t have a weak axis, making it a strong structure in compressive and pressure loading, while also not requiring supports when printing. This makes for an ideal and mechanically sound infill.
And since the heat exchanger core is one continuous structure, it has improved fatigue life. There’s no need for brazing, welding, or other such techniques to assemble.
Fluid management techniques
Optimized fluid flow
TPMS and gyroid structures facilitate efficient fluid flow, helping to improve turbulence and thereby enhancing cooling and fluid distribution. In the TPMS/gyroid structure, engineers can modify cell size, either increasing or decreasing the surface area as needed. This geometrical adaptation optimizes fluid pathways, lowering resistance and improving heat transfer efficiency and fluid management. This increases efficiency and lowers operational costs without compromising system performance.
Enhanced mixing
If properly plenumed, TPMS and gyroid structures assist in fluid distribution. When combined with the shared surface area between the "hot" and "cold" sides, they help ensure stable temperatures and prevent hotspot development.
Optimizing plenum design
A refined plenum design can help optimize complex structures like TPMS in heat exchangers. It plays a pivotal role in directing and distributing fluid flow while reducing pressure drops, thereby enhancing efficiency.
The precise shaping of the plenum is essential to achieve optimal fluid dynamics, with designs targeting consistent flow and high velocity inside the heat exchanger core. Variations in the plenum's flow area can influence pressure drop and fluid distribution, requiring meticulous planning for the perfect configuration.
nTop integrates with platforms like Ansys Discovery and other CAE tools such as Ansys Fluent and Simcenter StarCCM. This makes designing and refining heat exchangers — especially those with TPMS structures — a seamless process. With these advanced tools, engineers can tailor plenum shapes and fluid dynamics, ensuring consistent flow and reduced pressure drops. This approach significantly boosts thermal performance.
Manipulating different design parameters
Baffles
Baffles play a crucial role in directing fluid flow, extending the fluid's dwelling time inside the heat exchanger, and enhancing heat transfer efficacy. However, adding more physical baffles can significantly increase pressure drop, with fluids needing more energy to navigate these obstacles.
To tackle this, nTop allows for the concept of virtual baffles, addressing the pressure drop issue by enabling engineers to modify the heat exchanger core's structure at specific points, creating a "choke point" to guide fluid flow. This not only ensures prolonged fluid contact for efficient heat transfer, but also avoids the significant pressure drop associated with traditional baffles.
Mid-surface offset
A crucial parameter in heat exchanger lattice design is the mid-surface offset. This parameter enables engineers to finely adjust the flow area in both the hot and cold channels, primarily focused on reducing pressure drop. With nTop, engineers gain precise control, facilitating subtle modifications to the lattice structure. This fine-tuning optimizes fluid flow areas, enhancing fluid movement, and potentially increasing heat transfer efficiency.
Design space shaping
Rather than starting with fixed designs, this novel approach uses computational fluid dynamics (CFD) data in the early design stages. Engineers can use nTop to study the natural fluid dynamics in the intended design space or volume without any predefined heat exchanger elements. This enables them to mold the heat exchanger core based on specific thermal flow areas, leading to designs that directly influence pressure drop. It offers a more customized start to thermal management before progressing to intricate design facets.
Reshaping plumbing geometry for fluid management
Engineers are adopting novel methods to optimize plumbing geometry for enhanced fluid management in modern heat exchangers. The process begins with an in-depth analysis, incorporating key design factors such as velocity data points. These data points are then converted into a format compatible with nTop. This allows engineers to target and eliminate low-velocity zones, promoting uniform fluid flow and better energy efficiency.
To counteract energy losses primarily caused by sharp turns and uneven surfaces in the plumbing, engineers are reshaping geometries to bolster energy conservation within the system. By adjusting how fluid gets to and first interacts with the heat exchanger core, significant energy savings can be achieved.
Designing the future of aerospace and defense with nTop
Additive manufacturing is reshaping the aerospace and defense landscape, bringing a new era in heat exchanger design. Coupled with the capabilities of AM and next-gen software like nTop, engineers are experiencing unprecedented design flexibility and performance gains.
nTop stands at the forefront of engineering design software. It not only supports the development of innovative thermal management and fluid flow setups, but also accelerates and automates the design iteration process. This speed allows engineers to rapidly test and refine multiple versions of a design, pinpointing the most efficient structures in a shorter timeframe and setting new standards in the aerospace and defense sector.
To learn more, take a look at our guide on heat exchangers for aerospace and defense.
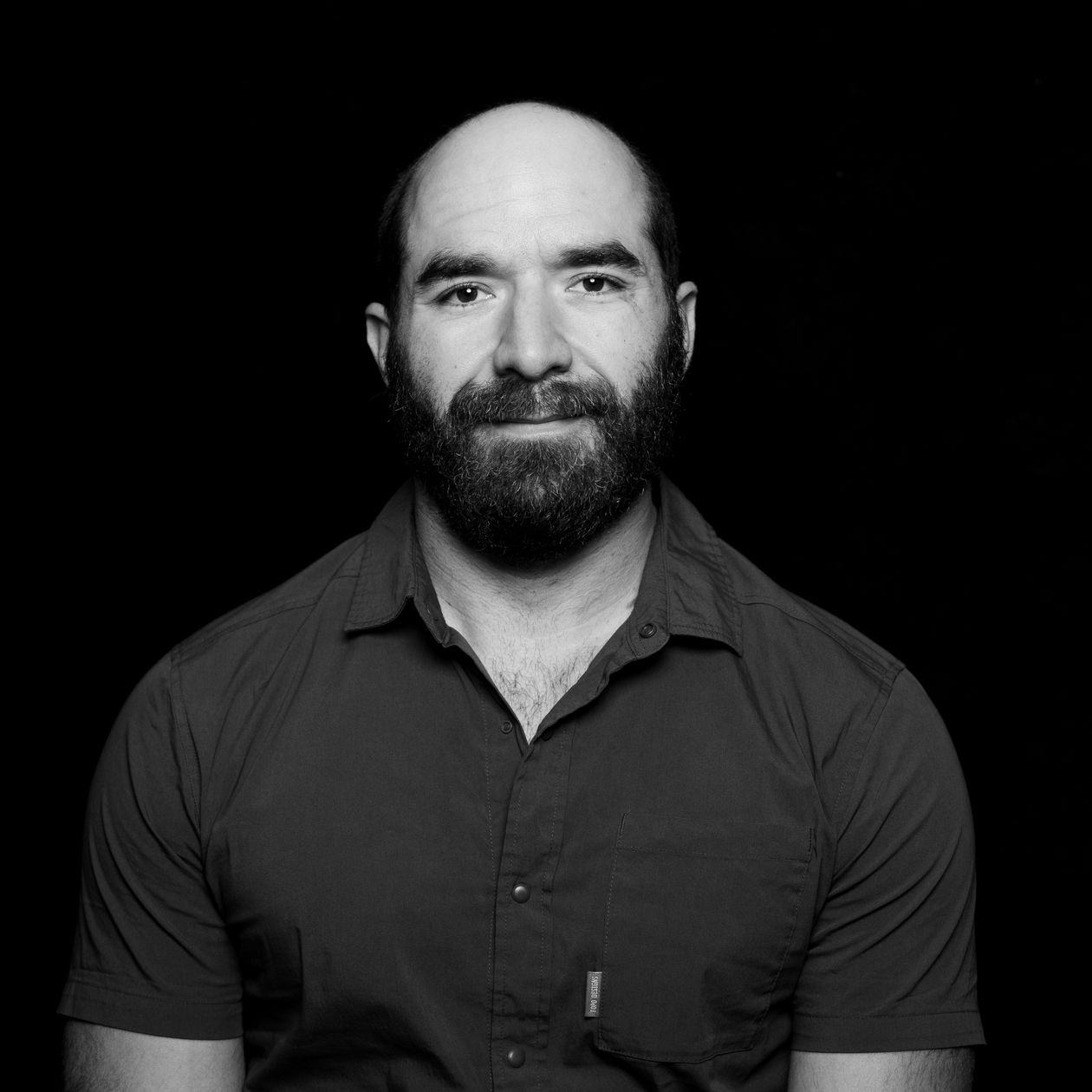
Maiki Vlahinos
Maiki Vlahinos is a Staff Solutions Engineer at nTop. His primary focus is solving new unique and difficult problems in the Aerospace & Defense Industries. Vlahinos has over a decade of CAE expertise in CAD, FEA, CFD and Optimization. Most recently, his focus has been on innovative design efforts for heat exchangers and fluid domain topologies utilizing CFD Simulation Results before any geometry has been built or generated. Most recently he presented at the 5th Global Webinar on 3D Printing and Additive Manufacturing on Automating Design Exploration for Implicit Geometries.
Related content
- VIDEO
Five ways to lightweight in nTop
- VIDEO
Topology Optimization Design for Cast and Injection-Molded Parts
- VIDEO
Lightweighting an impeller for additive manufacturing
- GUIDE
Download: Advanced design software and additive manufacturing for personalized implants
- VIDEO
Sneak peek into the nTop + Autodesk Fusion 360 integration